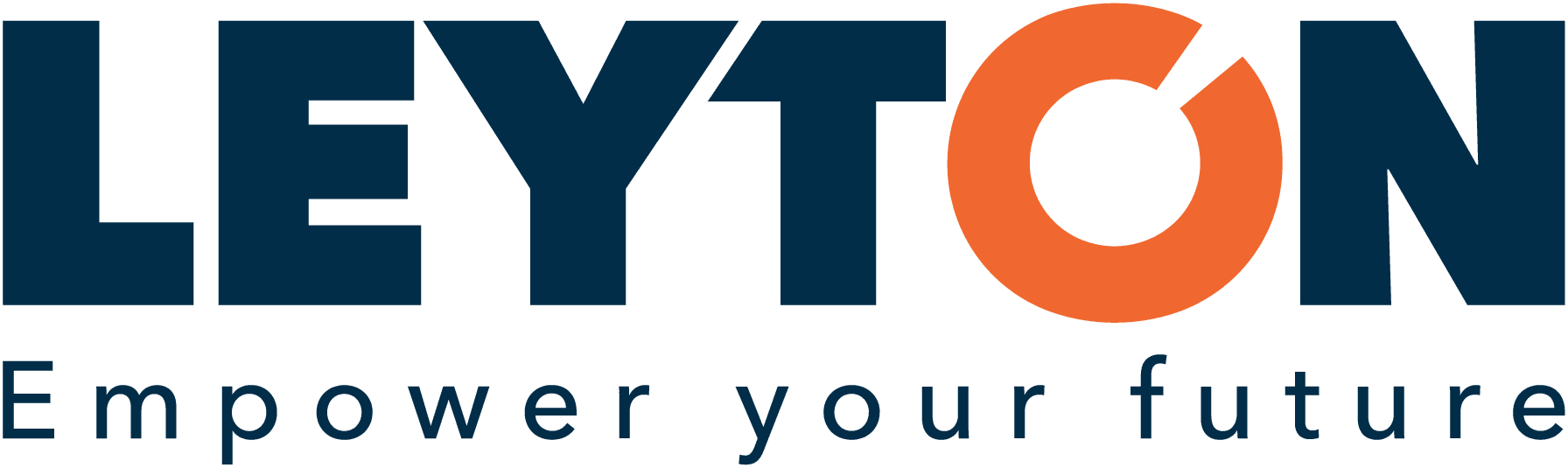
Building Ireland’s Future: How MMC is Revolutionising Construction
Introduction
The construction industry stands at a pivotal crossroads, with Modern Methods of Construction (MMC) rapidly transforming traditional building practices. As the demand for efficient, sustainable, and cost-effective construction solutions continues to grow across Ireland, MMC offers a compelling pathway forward. Factory production, digital design tools, and new materials are changing the daily work of every construction professional. For consulting engineers specifically, this shift demands new skills but offers substantial benefits in project delivery. In Ireland specifically, the housing shortage and climate commitments require construction solutions that deliver more buildings with fewer resources and lower emissions. MMC addresses these twin challenges directly.
The Technological Forerunner
The acceleration of technological innovation within MMC is remarkable. 3D volumetric construction has matured significantly, enabling entire room units to be manufactured with precision in controlled factory environments before transportation to the site. This approach dramatically reduces construction timelines while maintaining exceptional quality standards. Meanwhile, modular building techniques have evolved beyond simple repetitive structures to accommodate complex architectural designs that were previously thought impossible without traditional methods.
Twin wall technology represents one of the most promising hybrid methods gaining traction in Ireland. This technology consists of two precast concrete panels connected by steel lattice girders, with the void between them filled with in-situ concrete on-site. Engineering studies have demonstrated that interface shear strength increases with surface roughness, outer biscuit concrete strength, and connector embedment depth. The use of lattice shear connectors and increasing their depth significantly improves stiffness, flexural failure load, and composite action. Recent finite element modelling has confirmed that single trusses can
replace double trusses without compromising performance under certain conditions. A finding that offers significant material efficiency gains.
Twin wall systems significantly outperform traditional methods in critical areas that matter to consulting engineers: they carry heavier loads while using less material, provide better sound insulation between dwellings (a common complaint in multi-unit housing), and achieve fire ratings that satisfy the most stringent regulations without additional treatments. These systems have proven themselves in both residential and commercial applications across Ireland, offering a versatile solution that bridges prefabrication efficiency with structural performance.
Digital integration through Building Information Modelling (BIM) has become the backbone of successful MMC implementation, creating a seamless information flow from design through manufacturing to assembly. For consulting engineers, this digital thread offers unprecedented opportunities to optimise designs, predict performance, and collaborate across disciplines with greater efficiency.
Sustainability at the Core
MMC’s sustainability credentials extend far beyond the obvious reduction in construction waste. The factory-based production model enables precise resource management and material optimisation that would be impossible to achieve on traditional construction sites. Studies indicate that MMC approaches can reduce material waste by up to 90% compared to traditional construction methods.
The controlled manufacturing environment also facilitates the integration of cutting-edge insulation technologies and airtightness solutions, resulting in buildings that significantly outperform their traditionally built counterparts in energy efficiency. Twin wall systems, for instance, can be engineered with precise thermal breaks and integrated insulation layers, achieving U-values as impressive as 0.12W/m²K, far exceeding regulatory requirements while using less material. This performance advantage aligns perfectly with Ireland’s ambitious climate action goals and provides consulting engineers with powerful tools to deliver on increasingly stringent building regulations.
Challenges and Opportunities for Irish Engineering Consultants
While MMC presents tremendous opportunities, Irish consulting engineers must navigate several technical challenges during this transition. The integration of modular components with traditional building systems requires careful consideration of load paths, connections,
and material interfaces. Modular dimensions are often restricted by transportation regulations, which can limit design flexibility. Furthermore, the seamless integration of building services (plumbing, electrical, and HVAC systems) within modular units requires detailed planning to avoid rework on-site.
For twin wall systems specifically, engineers must understand the complex interaction between precast elements and in-situ concrete, including calculating differential shrinkage, managing thermal bridging at connections, and ensuring dimensional precision for factory production. Structural connections between modular units and traditional structures are particularly critical for stability under dynamic loads like wind or seismic activity.
However, these challenges represent opportunities for forward-thinking firms to differentiate themselves in an evolving marketplace. The Shanganagh Castle Estate project in Dublin demonstrates the efficiency gains possible with MMC approaches. This large-scale development, which commenced in September 2022, implemented a phased delivery approach using prefabricated elements, including twin wall technology. Phase 1, comprising 51 houses and a creche, was completed in just 14 months by September 2024. The subsequent phases of apartment construction are progressing at an 18-month timeline per phase, which is remarkably efficient for developments of this scale. This project also earned distinction as Ireland’s largest passive house scheme, demonstrating the compatibility of MMC with the highest sustainability standards.
The economic advantages are equally compelling. Research indicates that MMC techniques can accelerate construction timelines by 20% to 60% compared to traditional methods. In the context of rising construction costs, with tender prices increasing by 8.9% in 2021, 3.5% in 2022, and 1.6% in 2023, this efficiency is invaluable. Studies have identified potential cost savings of up to 14% for two-bedroom apartments through a combination of approaches, including the adoption of European construction methods like twin wall systems.
The firms that successfully integrate MMC knowledge into their practice will find themselves well-positioned to deliver on the Housing for All strategy’s ambitious targets while maintaining the highest standards of quality and sustainability. Furthermore, the precision and predictability inherent in MMC approaches allow engineers to push the boundaries of design innovation while maintaining confidence in structural performance and longevity.
Looking Forward
As Ireland continues to address its housing and infrastructure needs, MMC will play an increasingly central role in delivering solutions that are not only faster and more cost-effective but also more sustainable and adaptable to future needs. The adaptation of Irish building codes to accommodate these innovative construction methods, particularly regarding energy efficiency, fire safety, and structural performance, created a supportive regulatory environment for MMC adoption.
Quality assurance processes for MMC components have also evolved, with regular inspections during manufacturing, rigorous testing of structural elements, and adherence to Eurocodes ensuring that components perform as designed under Irish conditions. Digital tools like BIM are increasingly used to track quality throughout the design-to-installation process, providing engineers with unprecedented visibility into component performance.
For consulting engineers, embracing these methods represents an opportunity to lead rather than follow in the industry’s transformation. The technical expertise required to optimise twin wall systems, flat slab construction, and other emerging hybrid methods will become increasingly valuable as the industry transitions from traditional approaches.
I will be speaking on these topics and more at the National Construction Summit at the National Sports Campus (Dublin) on the 2nd of April, focusing specifically on how Modern Methods of Construction are reshaping the industry’s future. As an R&D tax consultant working extensively with construction firms and MMC specialists, I look forward to sharing deeper insights into how engineering innovation is driving this revolution.
Article by Benson John MSc CEng MIMeche,
Assistant Manager – R&D Tax Incentives